Understanding Bridge City’s Economic Landscape
Bridge City’s robust economic growth presents significant opportunities for businesses across multiple sectors. Key infrastructure developments and strong market demand create an ideal environment for business expansion, particularly in construction, manufacturing, and logistics services.
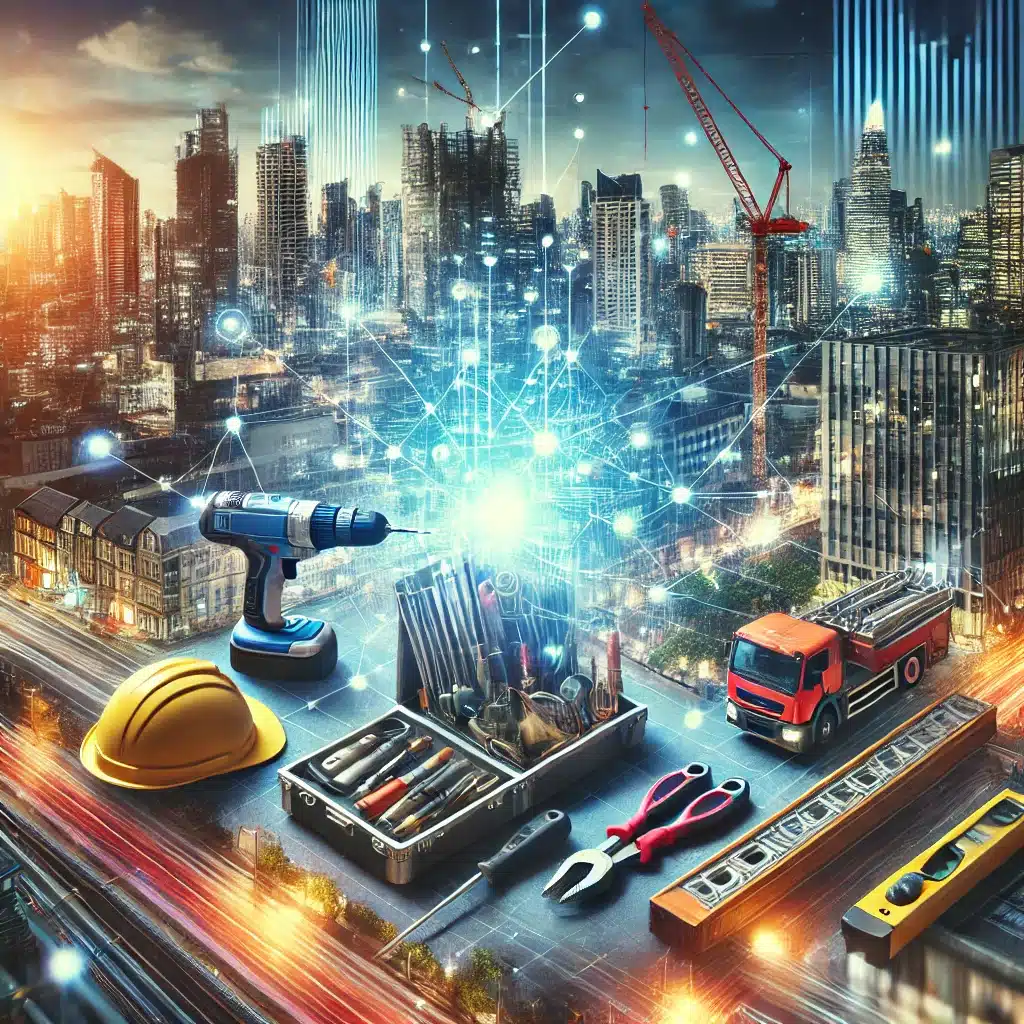
Current Growth Sectors and Opportunities
Bridge City’s construction sector has experienced a 15% year-over-year growth, driven by commercial development and infrastructure projects. The industrial corridor expansion along the riverfront has created unprecedented demand for construction equipment and related services.
Manufacturing and logistics have emerged as secondary growth drivers, with the new industrial park attracting major regional players. This diversification offers equipment suppliers multiple revenue streams and partnership opportunities across various business segments.
Local Infrastructure Advantages
The city’s strategic location, connected by three major highways and a modernized port facility, provides excellent logistics accessibility for equipment delivery and maintenance. The recently upgraded power grid ensures reliable operations for heavy machinery and industrial equipment.
Bridge City’s Industrial Development Zone offers tax incentives and streamlined permitting processes for businesses investing in capital equipment. The zone’s modern infrastructure includes high-capacity power lines, fiber optic networks, and specialized waste management facilities.
Market Demand Analysis
Recent market studies indicate a 40% increase in demand for specialized construction and maintenance equipment in Bridge City. The following table illustrates key demand patterns:
Equipment Category | Growth Rate | Primary Drivers |
---|---|---|
Heavy Construction | 40% | Infrastructure Projects |
Maintenance Tools | 35% | Factory Expansions |
Safety Equipment | 25% | Regulatory Requirements |
Local businesses report significant backlogs in equipment availability, particularly for specialized machinery and high-capacity tools. This gap represents a prime opportunity for equipment suppliers and rental services.
Essential Equipment for Business Success
Success in Bridge City’s competitive market requires strategic equipment selection focusing on quality, efficiency, and compliance. The right mix of construction, maintenance, and safety equipment forms the foundation of operational excellence.
Construction and Site Development Tools
Core equipment needs vary by project scale but typically include excavators, loaders, and concrete handling equipment. National Site Supplies offers comprehensive packages tailored to project specifications and duration.
Essential site development tools include:
- Earth moving equipment
- Material handlers
- Concrete processing tools
- Surveying equipment
- Temporary power solutions
Maintenance and Repair Equipment
Regular maintenance requires both specialized tools and general-purpose equipment. Investment in quality maintenance equipment typically reduces downtime by 30-40% compared to using basic tools.
Key maintenance categories include:
- Diagnostic equipment
- Precision measurement tools
- Power tools and accessories
- Specialized repair kits
- Calibration equipment
Safety and Compliance Tools
OSHA-compliant safety equipment is mandatory for all construction and industrial operations. Standard safety packages should include personal protective equipment (PPE), fall protection systems, and emergency response kits.
Environmental monitoring tools and safety signage systems complete the basic safety infrastructure. These systems help maintain compliance while protecting workers and reducing liability risks.
Strategic Equipment Procurement
Effective procurement strategies balance immediate needs with long-term value. Understanding lease options, building strong supplier relationships, and implementing robust inventory management systems are critical for optimizing equipment investments.
Purchase vs. Leasing Considerations
Equipment acquisition decisions should align with project timelines and capital availability. For equipment used more than 70% of the time, purchasing often provides better long-term value, while leasing offers flexibility for specialized or intermittent needs.
Cost comparison matrix for common equipment:
Equipment Type | Purchase ROI Timeline | Lease Advantage Threshold |
---|---|---|
Heavy Machinery | 3-5 years | <60% usage rate |
Power Tools | 1-2 years | <50% usage rate |
Specialty Equipment | 4-6 years | <40% usage rate |
Supplier Selection and Relationships
Vendor evaluation criteria should include equipment quality, maintenance support, and parts availability. National Site Supplies maintains a 98% parts availability rate and offers 24/7 technical support for all major equipment categories, setting an industry benchmark for supplier reliability.
Key supplier selection factors:
- Equipment reliability ratings
- Maintenance service coverage
- Parts availability guarantees
- Technical support quality
- Financial stability
Inventory Management Systems
Modern inventory tracking systems reduce equipment downtime and optimize utilization rates. Cloud-based management platforms offer real-time visibility and maintenance scheduling capabilities.
Implementation of digital inventory systems typically results in:
- 25% reduction in equipment downtime
- 30% improvement in utilization rates
- 20% decrease in maintenance costs
Maximizing ROI Through Equipment Optimization
Equipment optimization requires systematic maintenance, performance monitoring, and strategic cost management. Proper implementation of these practices can increase equipment lifespan by 40% while reducing operational costs.
Maintenance and Lifecycle Management
Preventive maintenance programs should follow manufacturer specifications while accommodating local operating conditions. Regular maintenance intervals typically cost 30% less than reactive repairs and extend equipment life significantly.
A comprehensive maintenance schedule includes:
- Daily operational checks
- Weekly performance monitoring
- Monthly system assessments
- Quarterly major inspections
- Annual overhauls
Equipment Efficiency Metrics
Key Performance Indicators (KPIs) for equipment efficiency include:
Metric | Target Range | Impact Factor |
---|---|---|
Utilization Rate | >85% | Revenue Generation |
Downtime | <5% | Operational Costs |
Maintenance Ratio | 2-5% | Equipment Longevity |
Monitoring these metrics helps identify optimization opportunities and justify equipment investments.
Cost Recovery Strategies
Equipment cost allocation should reflect actual usage patterns and include all operating expenses. Implementing usage-based charging systems can improve cost recovery by 25-35%.
Effective cost recovery mechanisms include:
- Project-based billing
- Hour-meter tracking
- Maintenance cost sharing
- Depreciation allocation
- Performance-based pricing
Compliance and Safety Standards
Meeting regulatory requirements is essential for business operations in Bridge City. Understanding and implementing proper safety standards not only ensures legal compliance but also enhances operational efficiency and worker protection.
Local Regulatory Requirements
Bridge City’s municipal code Chapter 453 outlines specific equipment requirements for construction and industrial operations. Compliance with these regulations requires regular equipment inspections and certification.
Key compliance areas include:
- Equipment noise levels (<85 dB during standard hours)
- Emissions standards for powered equipment
- Load capacity certifications
- Operator licensing requirements
- Equipment age restrictions (<10 years for heavy machinery)
Environmental Guidelines
Environmental compliance focuses on emissions control, waste management, and resource efficiency. Bridge City’s Green Business Initiative offers tax incentives for companies using eco-certified equipment.
Environmental requirements table:
Category | Requirement | Compliance Method |
---|---|---|
Emissions | Tier 4 Standards | Regular Testing |
Waste Management | Zero Runoff | Containment Systems |
Noise Control | <85 dB at property line | Sound Barriers |
Safety Certification Programs
OSHA-aligned safety programs must be implemented for all equipment operations. Certification requirements vary by equipment type and application, with renewal periods typically ranging from 1-3 years.
Essential certification elements:
- Operator training documentation
- Equipment inspection records
- Accident prevention protocols
- Emergency response procedures
- Safety audit compliance
Financial Planning for Equipment Investment
Strategic financial planning ensures sustainable equipment acquisition while maintaining healthy cash flow. Understanding available financing options and tax benefits helps optimize investment timing and structure.
Budgeting and Financing Options
Standard equipment financing structures include:
Option | Down Payment | Term Length | Best For |
---|---|---|---|
Bank Loan | 10-20% | 3-7 years | Long-term assets |
Equipment Lease | 0-10% | 2-5 years | Flexible needs |
Vendor Financing | 0-15% | 1-3 years | Quick acquisition |
The optimal financing mix typically combines multiple options to balance cash flow and ownership benefits.
Tax Benefits and Incentives
Section 179 deductions and bonus depreciation can significantly reduce the effective cost of equipment investments. Bridge City’s Enterprise Zone also offers additional tax credits for qualifying equipment purchases.
Key tax considerations:
- Immediate expensing options
- Depreciation schedules
- Local tax credits
- Energy efficiency rebates
- Environmental compliance incentives
Risk Management Strategies
Comprehensive risk mitigation should address both operational and financial risks. Insurance coverage should be matched to equipment value and usage patterns.
Essential risk management elements include:
- Equipment insurance coverage
- Performance bonds
- Liability protection
- Operator insurance
- Environmental liability coverage
Building Strong Supplier Relationships
Developing strategic partnerships with equipment suppliers ensures reliable access to equipment and support services. National Site Supplies offers comprehensive partnership programs designed for long-term collaboration.
Local Supplier Network Development
Supplier diversification helps ensure equipment availability and competitive pricing. Maintaining relationships with multiple suppliers provides backup options and broader equipment access.
Effective supplier network includes:
- Primary equipment vendors
- Specialty tool suppliers
- Parts distributors
- Service providers
- Technology partners
Service Level Agreements
Standard SLA components for equipment suppliers:
Service Type | Response Time | Coverage Hours |
---|---|---|
Emergency Repairs | 2-4 hours | 24/7 |
Regular Maintenance | 24-48 hours | Business hours |
Parts Delivery | Same day | Business hours |
Long-term Partnership Benefits
Strategic partnerships typically offer:
- Volume pricing discounts
- Priority service response
- Extended warranty coverage
- Training programs
- Technology updates
Future-Proofing Your Equipment Strategy
Anticipating future needs and industry trends ensures sustainable equipment investments. Focus on scalability, technology integration, and sustainability to maintain competitive advantage.
Technology Integration Opportunities
Digital transformation initiatives should focus on:
- Equipment telematics systems
- Predictive maintenance software
- Resource optimization tools
- Automated reporting systems
- Cloud-based management platforms
Scalability Considerations
Equipment strategies must accommodate growth:
- Modular equipment solutions
- Expandable capacity options
- Upgrade pathways
- Integration capabilities
- Future compatibility
Sustainable Equipment Solutions
Green equipment initiatives provide both environmental and economic benefits. Focus areas include:
- Electric/hybrid equipment options
- Energy efficiency improvements
- Waste reduction systems
- Renewable power integration
- Eco-friendly maintenance practices
This comprehensive approach to equipment management ensures Bridge City businesses can maintain competitive advantages while meeting regulatory requirements and environmental responsibilities.